Workholding equipment for 5-axis machining, Industry 4.0 applications and automation will be presented on the Roemheld group stand at the AMB show this year.
Zero point clamping
If workpieces have to be produced on different milling, grinding or eroding machines in succession and set-up times are to be minimised, zero-point clamping systems are ideal. On display for the first time will be the ‘SPEEDY connect’ double-acting, pneumatic, zero-point clamping system from Roemheld group member, Stark.
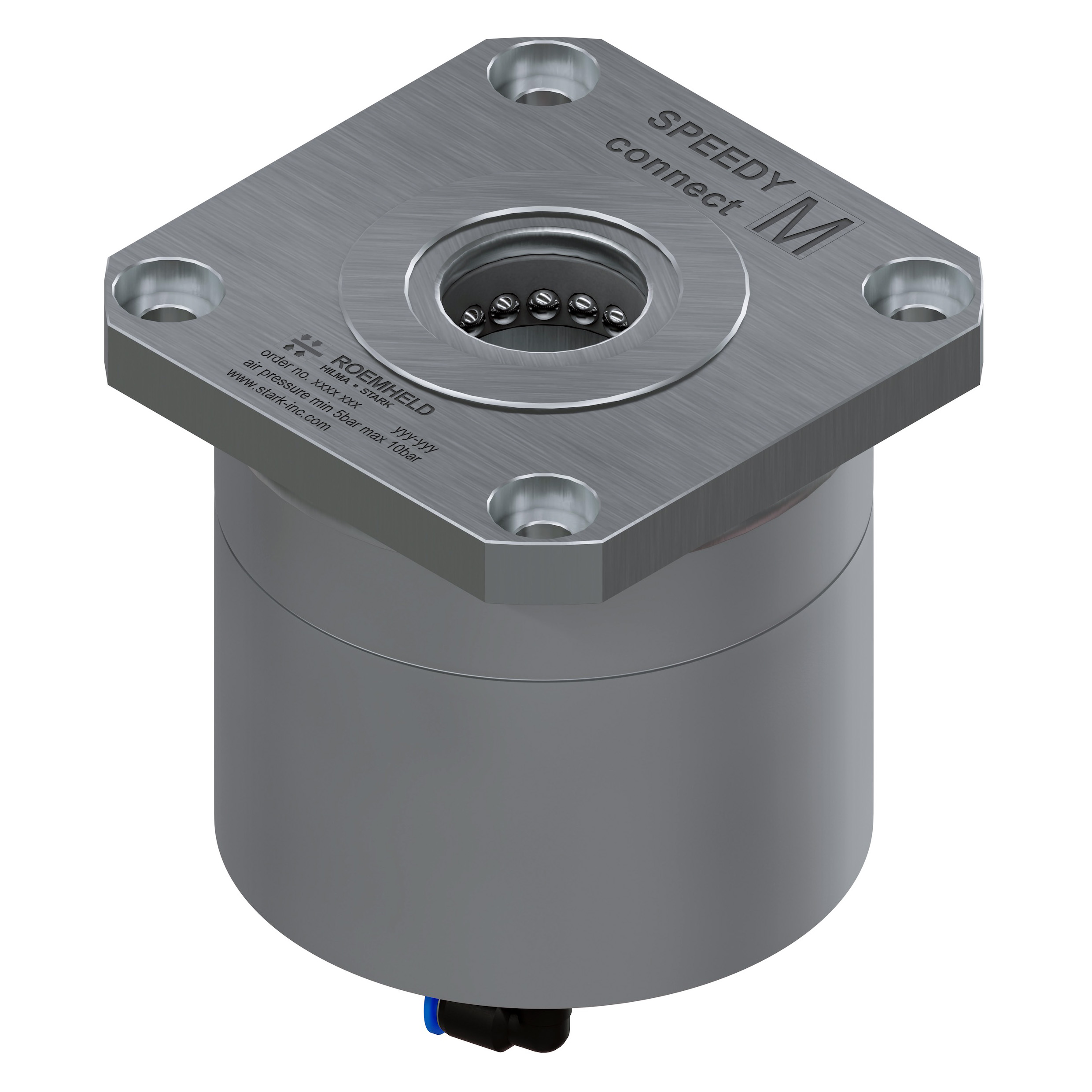
The new ‘SPEEDY connect’ Industry 4.0-compatible zero point clamping system from Stark will be launched at AMB 2018.
The units are compact, reliable and easy to automate, allowing their use in Industry 4.0 applications. Having a robust housing made of high quality tool steel and anodised, high-tensile aluminium, they can be used in harsh conditions including welding environments, such as for plant and vehicle construction.
The self-locking elements are clamped mechanically with springs, boosted pneumatically and also released pneumatically. Due to a 4.5 mm insertion stroke, a high insertion force of 3 kN at 5 bar or 8.5 kN at 20 bar and a retention force of 10 kN, the areas of application are varied and include robotic handling and gluing.
An integral electronic sensor indicates the current state of clamping via LEDs at the rear. The signals can be transmitted digitally to a higher level control system and clamp actuation can be integrated directly into a machine control.
Eccentric bore clamps
If components are to be held axially to save space, eccentric bore clamps from Roemheld are ideal. Their narrow design allows them to be placed close to workpiece contours. Workholding is effected inside the bore, leaving the exterior free for machining.
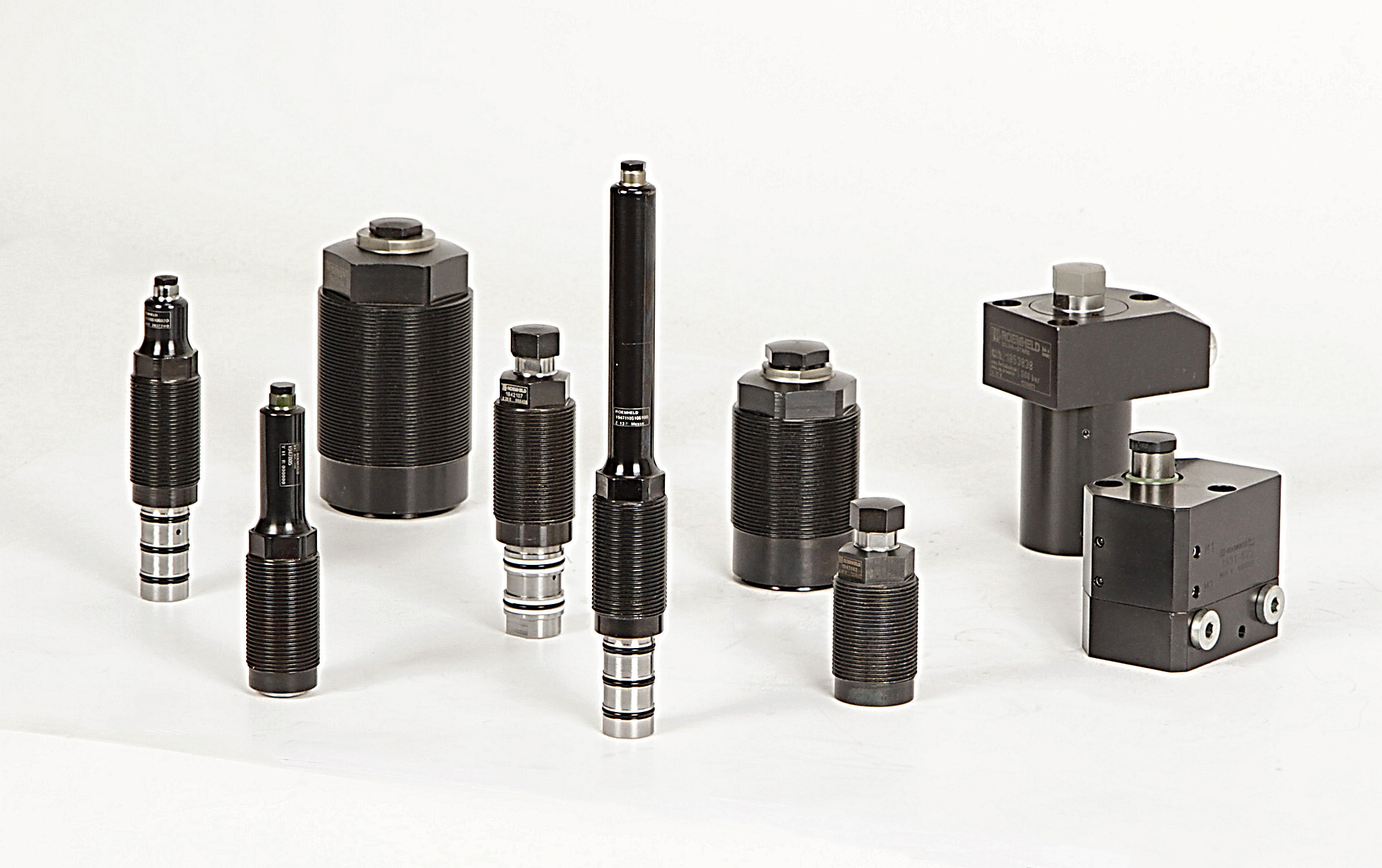
Supports from Roemheld help to prevent workpieces from vibrating or bending during machining.
Adjustment to bore size is achieved using bushings, which can be quickly exchanged by means of a bayonet lock. The clamping element remains in the fixture, a feature which Roemheld has applied to patent. Extensive monitoring options allow the use of the bore clamps in automated applications.
Hydraulic workpiece supports
Hydraulic workpiece supports from Roemheld are used wherever vibration or deflection of workpieces during machining must be avoided. A range of slim, threaded-body models is particularly versatile, being suitable for all installation positions and for use on low-pressure machines. Since the extension shaft can have a diameter of only 16 mm, even difficult-to-access areas of a component can be reached. Shaft length ranges from 20 to 100 mm.
The new threaded-body supports are protected by wipers. The double-acting variant, which clamps and unclamps hydraulically, is particularly suitable for automated production.
For operation of hydraulic clamping elements, Roemheld will show intelligent power units of new, modular design at AMB. An integrated condition monitoring system shows in real time such parameters as the current operating pressure, the fluid level, the temperature and the degree of contamination. Data can be fed back to the machine tool to support the manufacturing process. At the same time, the system helps to reduce downtime and assists planned maintenance.
Hilma workholding solutions
From another member of the Roemheld Group, Hilma, a tower clamping system from the TS series will be presented. It is designed for manual, semi-automatic or fully automatic operation on horizontal machining centres. Four, eight or 16 components may be clamped at the same time. The systems are available with a third-hand function for safely mounting pairs of components and in versions for heavy workpieces.
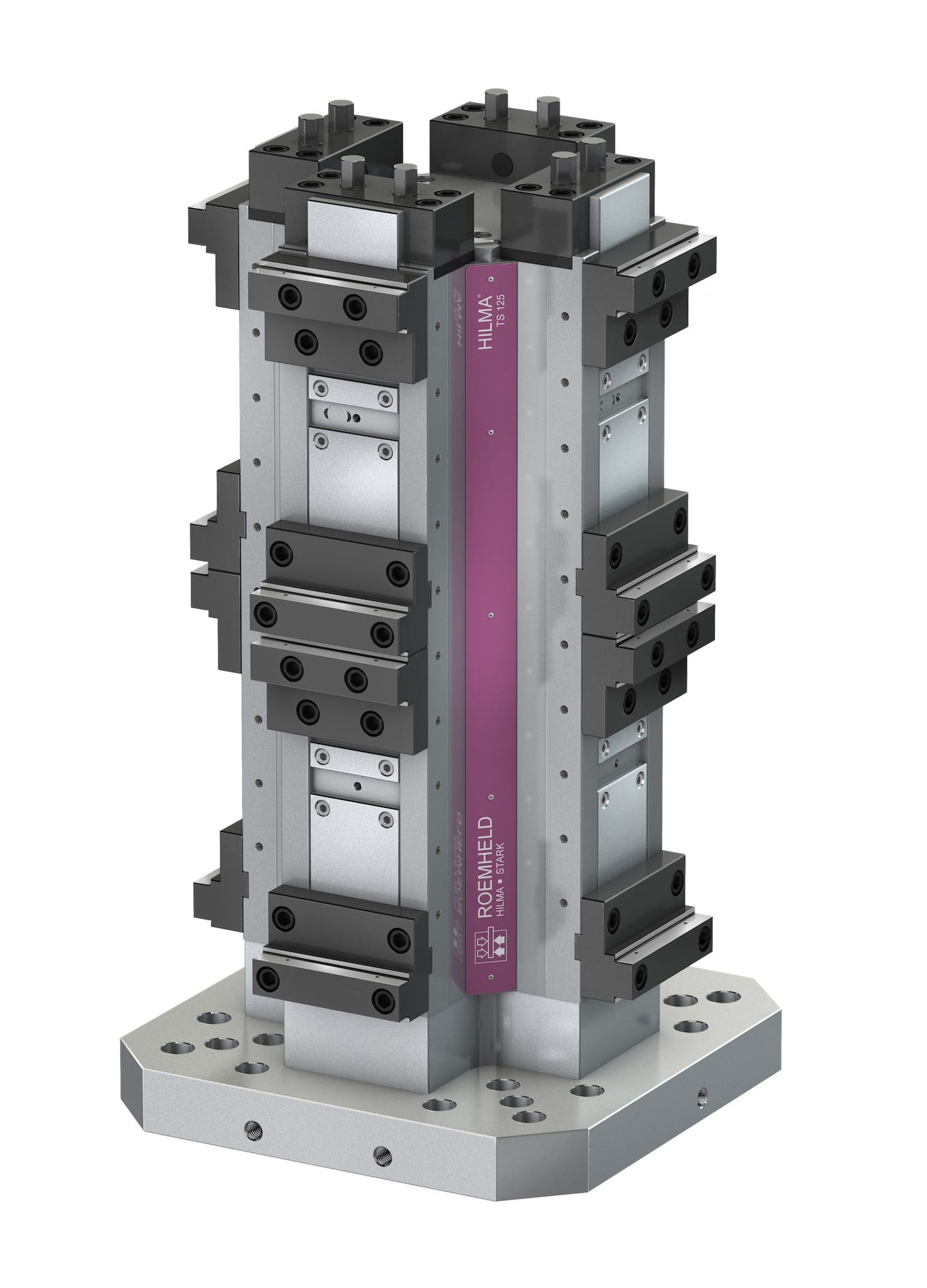
With tower clamping system in the Hilma TS series, up to 16 components can be clamped at the same time.
The Hilma TS H series complements the range of durable, high-precision, mechanical tower clamping systems with a hydraulic solution for automation. Since the models are identical in construction, the same extensive jaw range can be used. On each of the four sides, up to two workpieces of different dimensions can be hydraulically clamped and unclamped, manually, semi-automatically or fully-automatically. The clamping forces are monitored and controlled to suit automation. The hydraulics can be supplied either from above or through the machine table.
Vices from Hilma of the type Vario Line are used in vertical and horizontal applications and are flexibly adjusted to various workpiece sizes. This is ensured by magnetic quick-change jaws that can be replaced in a single operation. The machine vices may be configured individually and adapted to different machining tasks.
In evidence also on the stand at AMB will be Hilma MC-P vices, which are used mainly in 5-axis machining. Their compact design allows collision-free tool paths and the use of short standard tools. Three different types are available, whereby workpieces can be clamped concentrically, against a fixed jaw or positioned flexibly in the case of the ‘balance’ vice variant. The latter is particularly well suited to holding complex or delicate components without deformation. The sturdy design of the machine vices with integral swarf protection facilitates their use in pallet stations.
Leave A Comment
You must be logged in to post a comment.