Compact, highly adaptable clamping elements and sensor technology
Laubach, July 18, 2023. ROEMHELD will present solutions and components for production automation as well as adaptable clamping technology for the flexible set-up of workpieces at the EMO trade fair in Hanover, Germany.
The new, small version of the electric swing clamp and the tried and tested hydraulic swing clamps are extremely compact and now available for the first time with integrated pneumatic position monitoring.
Demos at the booth will showcase automation and Industry 4.0 applications, featuring various clamping elements that are equipped with extensive sensor technology. The new electrical media duct supports end-to-end clamping device digitalization and communication in these applications as well.
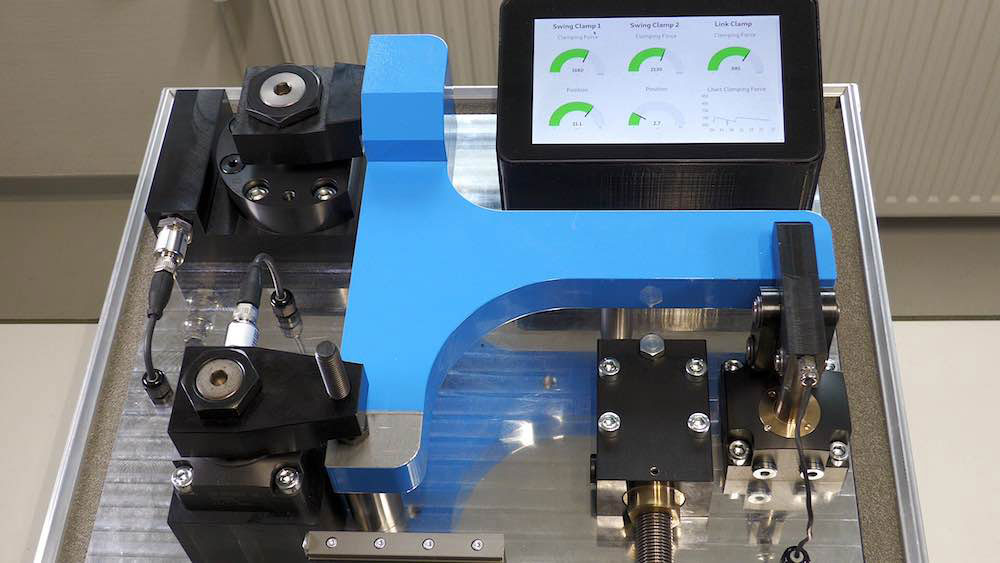
A demo at the ROEMHELD booth at the EMO will show different clamping elements such as hinge clamps, swing clamps, and bore clamps, equipped with extensive sensor technology for Industry 4.0 applications (photo: ROEMHELD)
ROEMHELD will also highlight solutions for the production automation of pallets and workpieces that even small and medium-sized companies can produce unmanned, efficiently and flexibly from batch size 1.
The HILMA.UC 125 concentric clamping machine vice will celebrate its trade fair premier. It enables a quicker changeover for different workpieces, so fewer clamping devices are needed for a wide range of clamping tasks. Visitors to the booth will also see the completely redesigned machine vices from the HILMA.NC product line.
ROEMHELD will present all its newest innovations, a selection from its extensive product range for clamping technology, as well as various customized clamping solutions at the EMO from September 18 to 23 in Hanover, Germany, at Booth E54 in Hall 4.
Small-size electromechanical swing clamp now available
ROEMHELD will feature a compact version of its established electric swing clamp designed for small installation spaces. It is the only electromechanical swing clamp available on the market to date. The axial pulling force of the small power package is 2.7 kN with a clamping stroke of 13 mm. An axial stroke of only 3 mm is required to swivel the clamp 180°.
Belleville springs facilitate mechanical reclamping so that precise clamping is achieved at all times. Various features and function controls also add to high process reliability. Safe operation is ensured thanks to the self-locking spindle drive. The clamping force is still maintained even if the energy supply is disconnected. For automation, all commands and information can be transmitted wirelessly via an optional IO-Link connection.
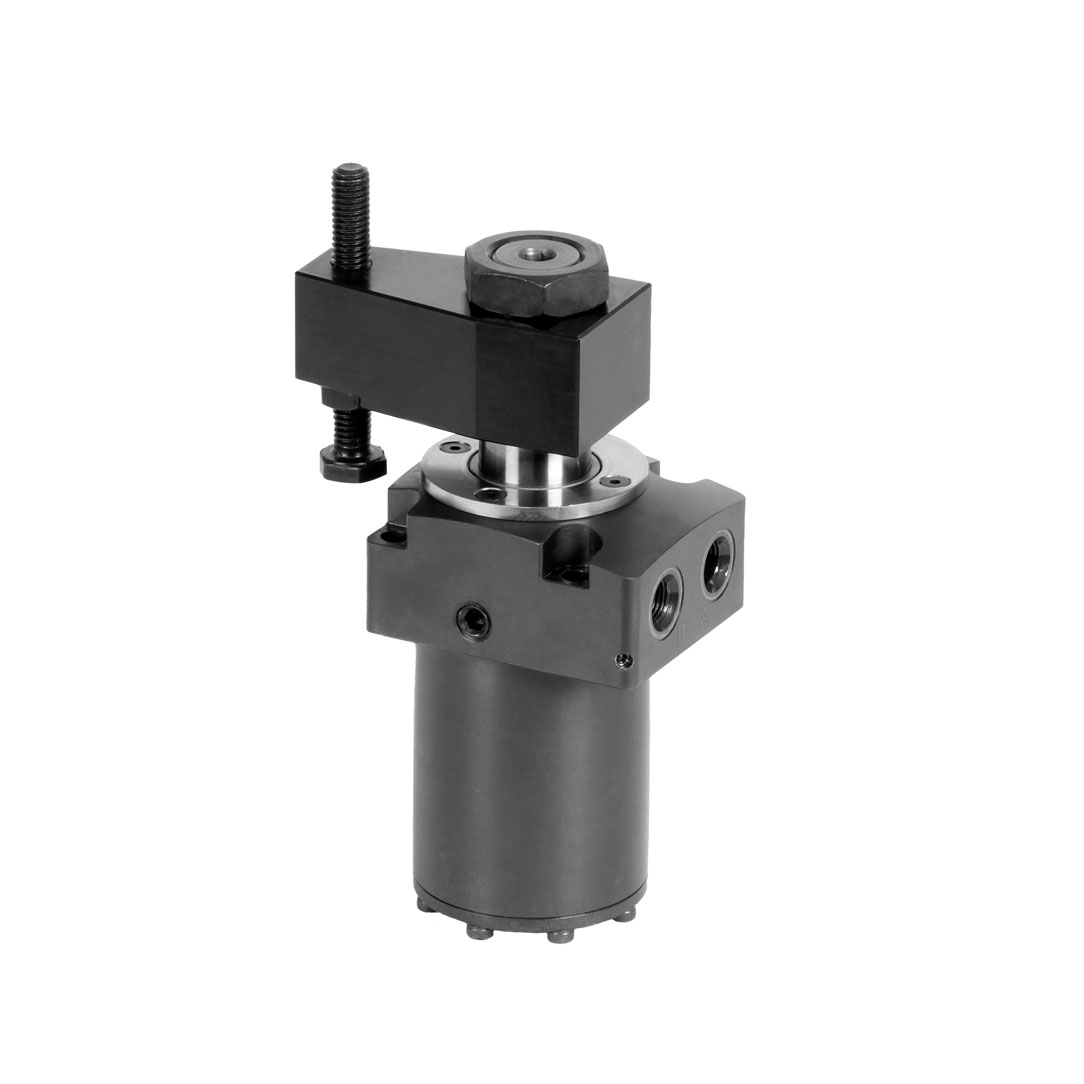
The tried and tested hydraulic swing clamps are still the same size, but are now available with integrated pneumatic position monitoring. This saves users space compared to the position monitoring previously offered (photo: ROEMHELD).
Space-saving integrated position monitoring for swing clamps
The models of the tried and tested hydraulic swing clamp series for operating pressures of 70 bar and 120 bar are also compact. Still the same size, they are now available with integrated pneumatic position monitoring, saving users space compared to the position monitoring previously offered. The double-acting elements with top flange are available in four sizes. Thanks to their compact design, they are partially recessible and achieve highly effective clamping forces of up to 13.3 kN even at an operating pressure of 70 bar.
Making clamping technology ready for Industry 4.0
At its booth, ROEMHELD will show how clamping technology meets the current and future requirements of Industry 4.0 applications. A demo will feature different clamping elements such as hinge clamps, swing clamps, and bore clamps, equipped with extensive sensor technology for Industry 4.0 applications.
For all elements, a display shows the respective stroke position, clamping force and clamping pressure. Integrated force, stroke and pressure sensors measure the values in real time and share the data. Other sensors for stroke and pressure monitoring and for checking the stroke position are also integrated in various components.
The sensor technology offers extensive information about the workpieces and fixtures clamped for machining. On the one hand, this ensures that a component is correctly and securely fixed for the manufacturing process. If errors are detected, it can be sorted out before machining. On the other hand, the quality of the workpieces can be continuously monitored and seamlessly documented during processing.
New electrical media duct for end-to-end digitisation
A media duct for electrical signals, especially for use on CNC machining centres, will be new to the trade show. A media duct was previously available only for oil and compressed air. This new innovation enables end-to-end digitisation and communication of all clamping devices. The electrical media duct is used on the STARK.intelligence modular sensor system, which can be employed to expand various zero point clamping systems for digital operation.
Zero point clamping systems connected to STARK.intelligence measure paths, positions, temperatures and pressures in real time, creating a status image of the clamping device. Furthermore, the information can be directly integrated into the machining process via an IO-Link interface and used for automation.
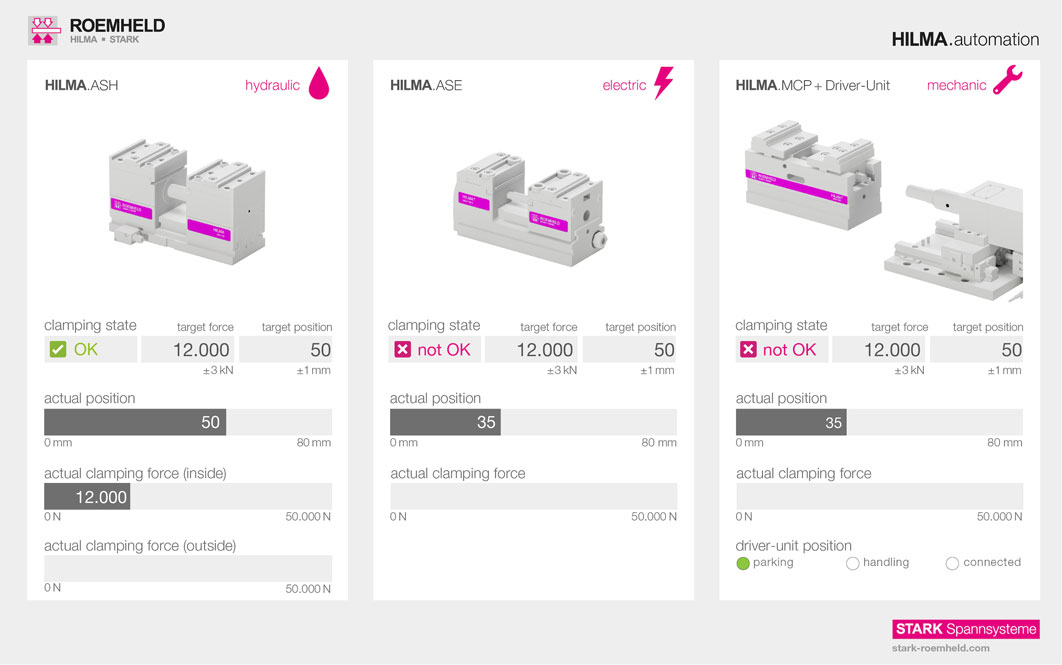
Automation cell with a complete solution of zero point clamping systems, vices and interfaces for unmanned production from batch size 1. The photo shows three different clamping systems: the hydraulic double-acting HILMA.ASH machine vice, the electric HILMA.ASE and the mechanical HILMA.MCP (photo: STARK).
Efficient production automation from batch size 1
With an automation cell, ROEMHELD offers various options for unmanned, efficient and flexible production of small quantities and many different components.
As alternative solutions the hydraulic double-acting HILMA.ASH machine vice, the electric HILMA.ASE and the mechanical HILMA.MCP will be shown in action side by side to highlight how ROEMHELD’s product range offers suitable automation solutions for every application and for different media availabilities. Continuous condition monitoring, uncompromising availability and high variability form the foundation of successful unmanned production.
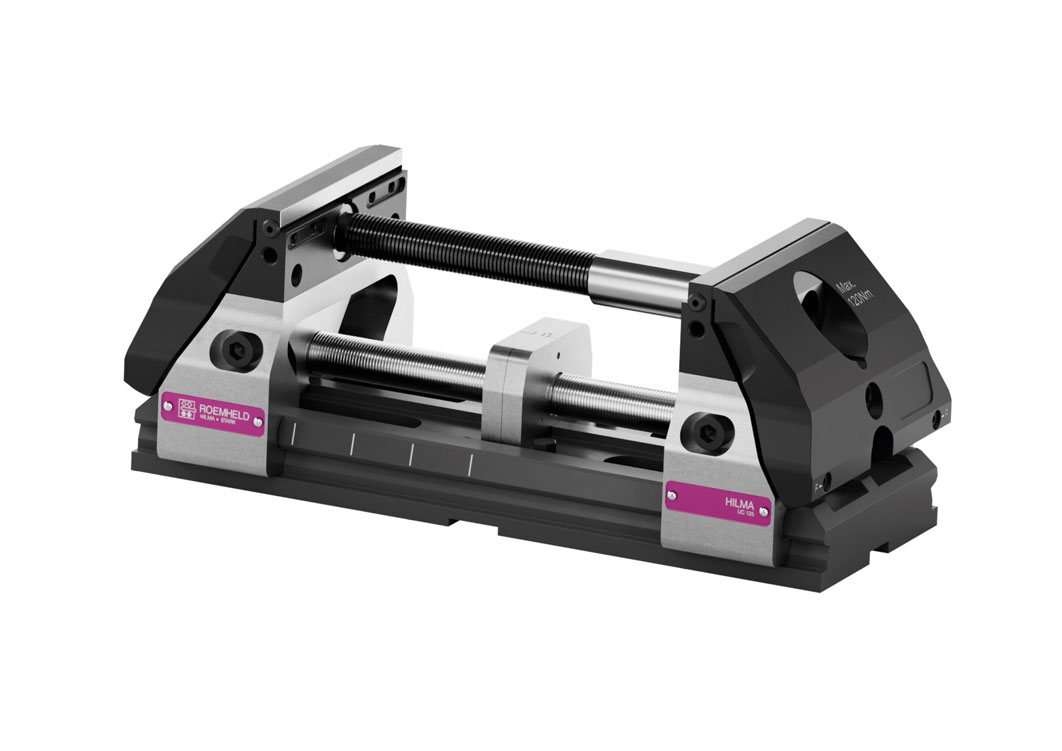
With the new HILMA.UC machine vice, users can convert vices for different workpieces more quickly, requiring fewer clamping devices (photo: STARK).
Universal and flexible: the new modular HILMA.UC 125 machine vice
The new concentric HILMA.UC 125 clamping machine vice is a highly variable clamping device for various clamping tasks that users can change over more quickly for different workpieces.
The clamping width can be expanded up to 600 mm in just a few steps. Different clamping jaws for blanks and finished parts as well as cubic and round workpieces are offered in the standard product line. This means that if production requirements change, further investment in new clamping devices is not required. The new product family can be perfectly combined with the existing zero point clamping systems to further increase flexibility.
The modular all-rounder for 3- to 5-axis machining also scores high marks with special clamping mechanics that prevent the clamp from shifting up and lifting the workpiece.
Completely redesigned HILMA.NC machine vices
The popular series of modular HILMA.NC machine vices will be on display at the EMO in their completely redesigned version. The clamping devices, which are used preferably on vertical machining centres, are available in two versions for different machining strategies and degrees of automation: as HILMA.NC, in which the clamping force is applied manually via crank handles, or as the hydraulically driven HILMA.NCH. Depending on the model, the mechanical version has a clamping force of up to 50 kN and a maximum of 63 kN with hydraulic actuation.
Thanks to their modular design, a wide range of accessories and different positioning and mounting options, HILMA.NC machine vices can be optimally adapted to different machining tasks, machines and environments. Jaw widths of 100, 125 and 160 mm are available, each with up to five standard overall lengths between 380 and 1,200 millimetres.
About the ROEMHELD Group
From medical engineering and mechanical engineering to the automotive, aerospace and agricultural industries or the production of smartphone cases: technologies and products of the companies in the ROEMHELD Group have been used to manufacture numerous industrial commodities and goods for end users for more than 80 years.
The ever-growing range of more than 25,000 catalogue items includes innovative and intelligent solutions for manual and automated clamping and set-up of dies, workpieces, fixtures and pallets as well as for handling and assembly. They are used by numerous industrial companies worldwide, especially in machining, forming technology, plastics processing and 3D printing.
The focus is always on efficiency and productivity — through minimum set-up times, fast manufacturing and high flexibility.
Innovation through tradition: ROEMHELD was established in 1707 with a foundry in Friedrichshütte, which still belongs to the ROEMHELD Group today and counts as one of Germany’s oldest active industrial businesses.
Three members belong to the owner-managed group of companies. Römheld GmbH Friedrichshütte, Laubach, Germany, is responsible for workholding elements, assembly and handling technology as well as die clamping and change technology. Zero point clamping systems, machine vices and tower workholding systems are produced by STARK Spannsysteme GmbH, Rankweil, Austria. Technical consulting and development of machine vices, tower workholding systems as well as die clamping and changing technology takes place at Hilma-Römheld GmbH in Wilnsdorf, Germany.
The Group employs around 530 people and is represented by service and sales companies in over 50 countries. It achieves an annual turnover of more than 90 million euros.
Visit Roemheld UK’s member profile to find out more.
Leave A Comment
You must be logged in to post a comment.