In Eltville am Rhein, Germany, Jean Müller develops and produces around 40,000 components for distributing, controlling, securing and measuring electrical energy in low-voltage networks. For handling particularly heavy punch press tools for manufacturing a new product series, the family-run business was initially looking for just a new transport cart. In the end, a complete die changing system was acquired from Roemheld, comprising racking and a lifting cart with integrated docking system and radio remote control. Similar technology is available in Britain and Ireland through Roemheld UK, Hitchin.
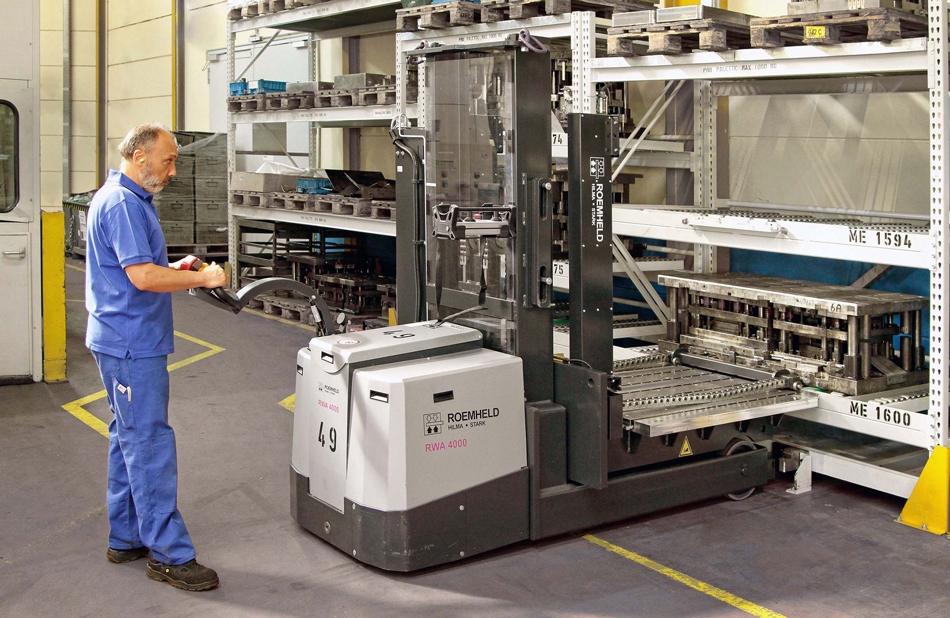
The Roemheld RWA 4000 transport cart in use at Jean Müller, Eltville am Rhein, about to pick up a die from the new racking.
Jean Müller makes and uses hundreds of tools for punching, injection moulding and injection compression moulding of products for customers mainly in Europe and Asia. Regular product innovations result in an ongoing requirement for new tools. One such new introduction was a Jean Müller Tokeo product range of larger strip-type fuse switch disconnectors. The department concerned was using a transport cart to move stamping tools around, but the maximum load was only 2.5 tonnes, too little to transport the large tools needed for producing the new Tokeo product.
Michael Gensecke, Jean Müller’s team leader for metal pre-products and design engineer Holger Christ started researching the market for a new cart with a higher load capacity. Ralf Depcik, head of production, set the direction: “We wanted the best solution, not the fastest. The aim was to find a transport cart for the heavy dies that would enable our presses to be set up quickly and safely.”
The cart also needed to be easy and ergonomic to operate, as there are several narrow locations in the factory with less than three metres of manoeuvring space around a 2.5-tonne Andritz Kaiser press and a 1.6-tonne Haulick Roos press. Furthermore, it was crucial that the dies could be inserted effortlessly and safely into the machine and racking at heights of between 300 and 1,800 mm. Finally, a remote control was desirable.
Mr Gensecke and his team shortlisted three potential suppliers, but none of the standard systems fulfilled all the requirements. A suitable solution was eventually proposed by Roemheld. Teams from both companies together developed a bespoke configuration that proved successful.
The heart of the joint solution is the manoeuvrable, electrically-driven Roemheld die changing cart type RWA 4000, capable of carrying a load of up to four tonnes. It has a die changing table with integrated hydraulic ball bars and a pull-push system that facilitates automatic insertion of the dies on a press bed.
During transport, the hydraulic balls in the cart table are lowered and consequently the die is prevented from slipping. A safety circuit ensures that the RWA 4000 only moves when the ball bars are retracted. Removable safety bars at the front and sides of the support surface additionally secure the die. The cart can be controlled from a central panel on the drawbar, on which a multi-function display is mounted. Alternatively, employees can adjust the most important cart functions remotely via the radio control.
The pull-push system integrated into the cart allows a die to be safely pulled by its eyelets from a storage rack onto the table. When it arrives at the press, the die is pushed onto the bed. Both motions require no physical effort from the operator. The complete system includes two rack systems with eight die locations, especially developed by Roemheld to store frequently-used dies close to the machine.
The system has been in continuous three-shift operation since the spring of 2022, the year Jean Müller celebrated its 125th anniversary. The distances the dies have to travel to the presses is now shorter, resulting in a time saving of 15 minutes for each changeover, which happens up to three times per shift.
Mevlüt Kücükler, who has been working as a setter on the presses for 32 years commented: “In the past, we had to lift a heavy die onto a press using a crane and forklift and position it manually. That was time-consuming and exhausting. Now changeover is easier, as nothing is moved manually any more. It’s much more convenient, faster, more practical and also very safe.”
Regarding the manufacturer’s cooperation with Roemheld, Mr Depcik concluded, “We have done good development work together, learned a lot from each other and achieved an excellent result. I am not sure whether this would have worked out so well with other suppliers.”
Visit Roemheld UK’s member profile to find out more.
Leave A Comment
You must be logged in to post a comment.