Applications extended from plastic injection moulding and rubber pressing to electromobility, wind farms, 3D printing, robotics and Industry 4.0
The Hilma division of German workholding specialist, Roemheld, has entered into a 50:50 joint venture (JV) with long-term co-operation partner, Rivi Magnetics, Sassuolo, Italy. The JV company, Roemheld Rivi GmbH based in Hilchenbach, Germany, intends to leverage both partners’ expertise to develop new applications for magnetic clamping technology and penetrate global markets more comprehensively.
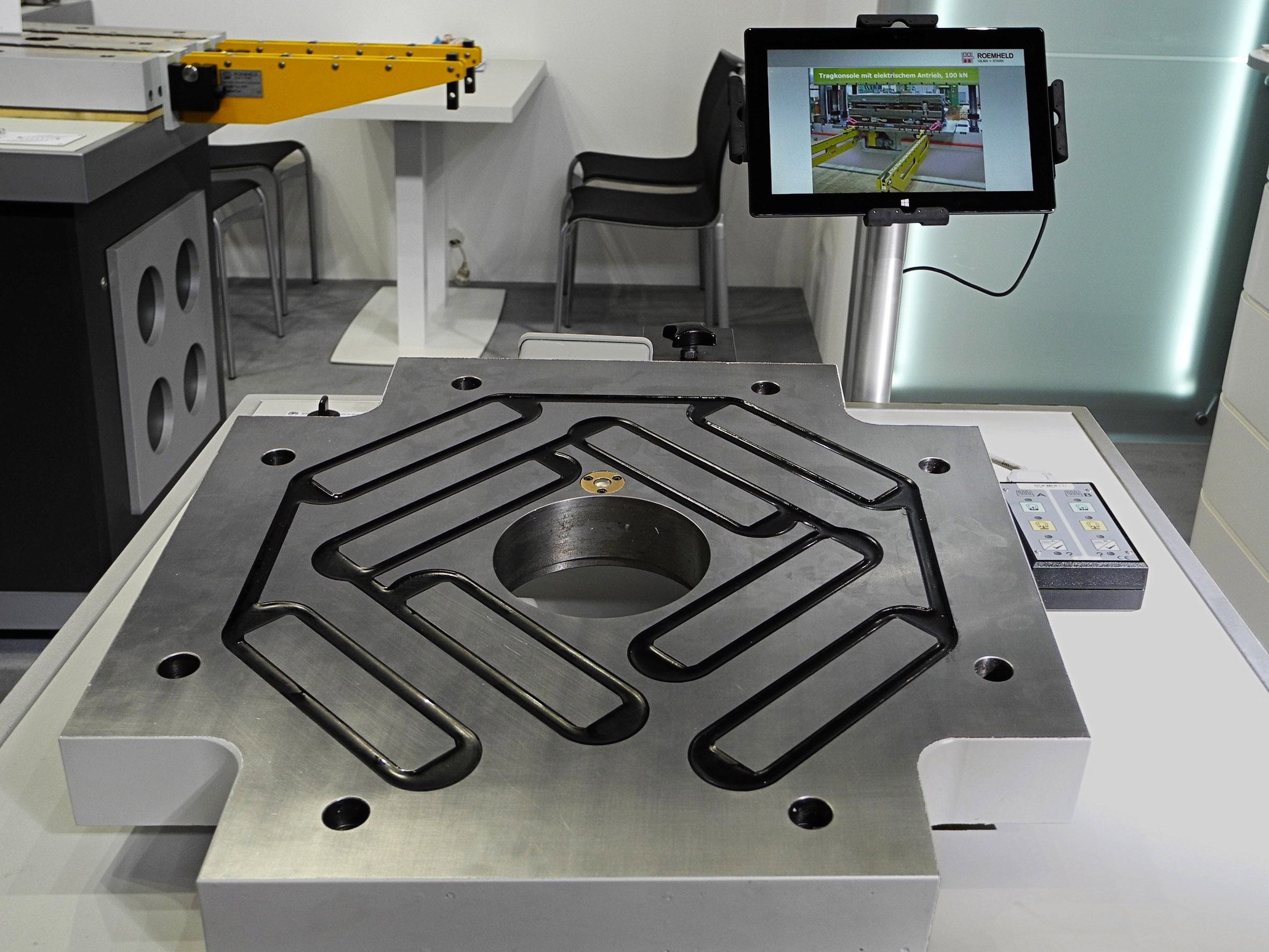
A joint venture company, Roemheld Rivi GmbH, has been formed to expand the co-operation partners’ magnetic clamping product range as well as the world markets into which they are sold.
Dual leadership of Roemheld Rivi is in the hands of Hans-Joachim Molka from the Roemheld management team, responsible for commercial matters and Davide Rivi, owner of Rivi Magnetics Srl, who is responsible for research and development.
Mr Molka commented, “We see a number of new opportunities in specific sectors in the coming years: drives for electromobility, 3D printing applications, locking mechanisms for rotors in wind turbines, and robotic assembly and handling. Magnetic clamping is aimed at customers working in the supply chains to these sectors, as well as at those looking for a partner for the implementation of Industry 4.0. ”
Mr Rivi added, “Magnetic clamping technology, with its many advantages in terms of set-up time optimisation, offers a huge market potential that we want to exploit even more. In addition to intensifying sales activities, Roemheld Rivi GmbH intends to launch a development initiative that will significantly broaden the product portfolio.”
Hilma M-TECS standard and customised magnetic clamping products are manufactured by Rivi Magnetics, the various models being capable of withstanding maximum temperatures of 80°C, 120°C or 240°C. There has been a noticeable increase in demand for quick mould clamping at the upper end of this temperature range. Systems can be either factory fitted by the machine manufacturer, or retrofitted to existing machines within a few hours.
Designed according to customer requirements with respect to weight (up to several tonnes), complexity of geometry and required clamping force, the systems are widely used in injection moulding and the rubber industry as well as in forming presses and stamping plants. The JV is still the only supplier of high-temperature magnetic clamping plates that can process both rubber and thermoplastics such as polyetheretheretherketone (PEEK) or polyphenylene sulfone (PPSU).
Mains current flow for just a few seconds is sufficient to ensure that nearly all moulds made of ferromagnetic materials are clamped over their entire surface. Without any further power drawn, uniform distribution of the clamping force ensures low wear. The moulds are subsequently released by a further short current pulse. The magnetic field generated by permanent magnets penetrates only a few millimetres into the mould and brings the two halves together precisely in terms of position and parallelility.
M-TECS products meet EN 201 and EN 289 standards for injection moulding machines and rubber presses. Requirements for feedback of magnetisation, power supply, mould monitoring and emergency stop are met and safety signals as well as error messages appear on the operating panel, all consistent with Industry 4.0 requirements.
Leave A Comment
You must be logged in to post a comment.