New hot stamping process not only reduces space requirements and costs, but also eliminates aging
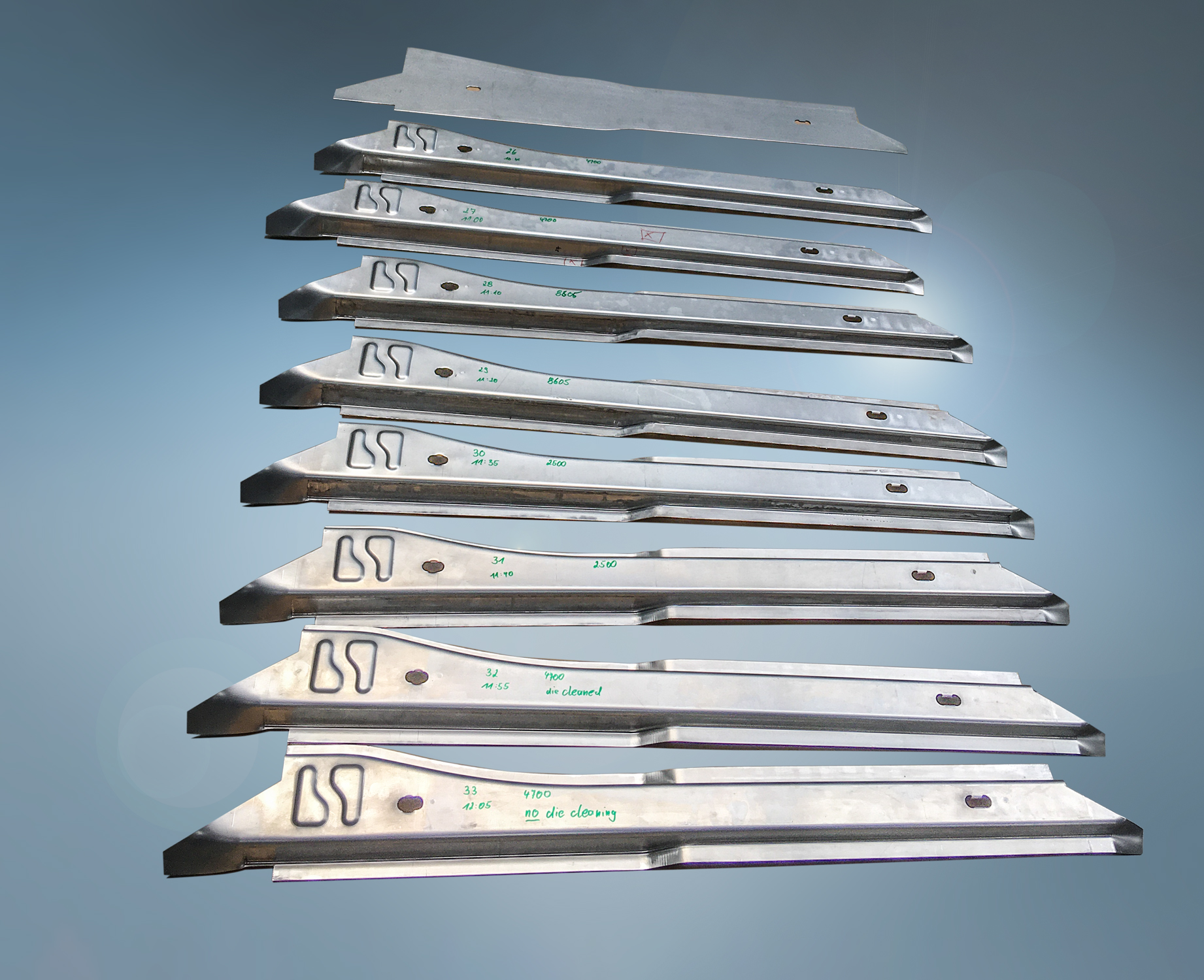
Parts made from high-strength aluminum sheets are increasingly being used in vehicles to save weight. © Schuler
Göppingen, September 20, 2023 – Parts made from high-strength aluminum sheets are increasingly being used in vehicles to save weight. Schuler now offers on its hydraulic presses a new process for hot stamping where the light metal is heated up very quickly by means of contact heating and formed in a water-cooled die. All process steps are performed in the die so, in contrast to the hot stamping of steel sheets, no separate furnace is required.
“This not only reduces the space requirements for the system, but also very significantly lowers the investment and operating costs,” explains Christian Palm, who is responsible for the hydraulic presses division at Schuler. “That makes hot stamping of aluminum a real alternative in sheet metal forming. The technology makes it possible to produce light and high-strength parts with a significantly higher degree of forming compared to cold forming, and offers a much greater scope for design.” Highly complex geometries and a tensile strength of 300 to 400 newton per square millimeter can be achieved.
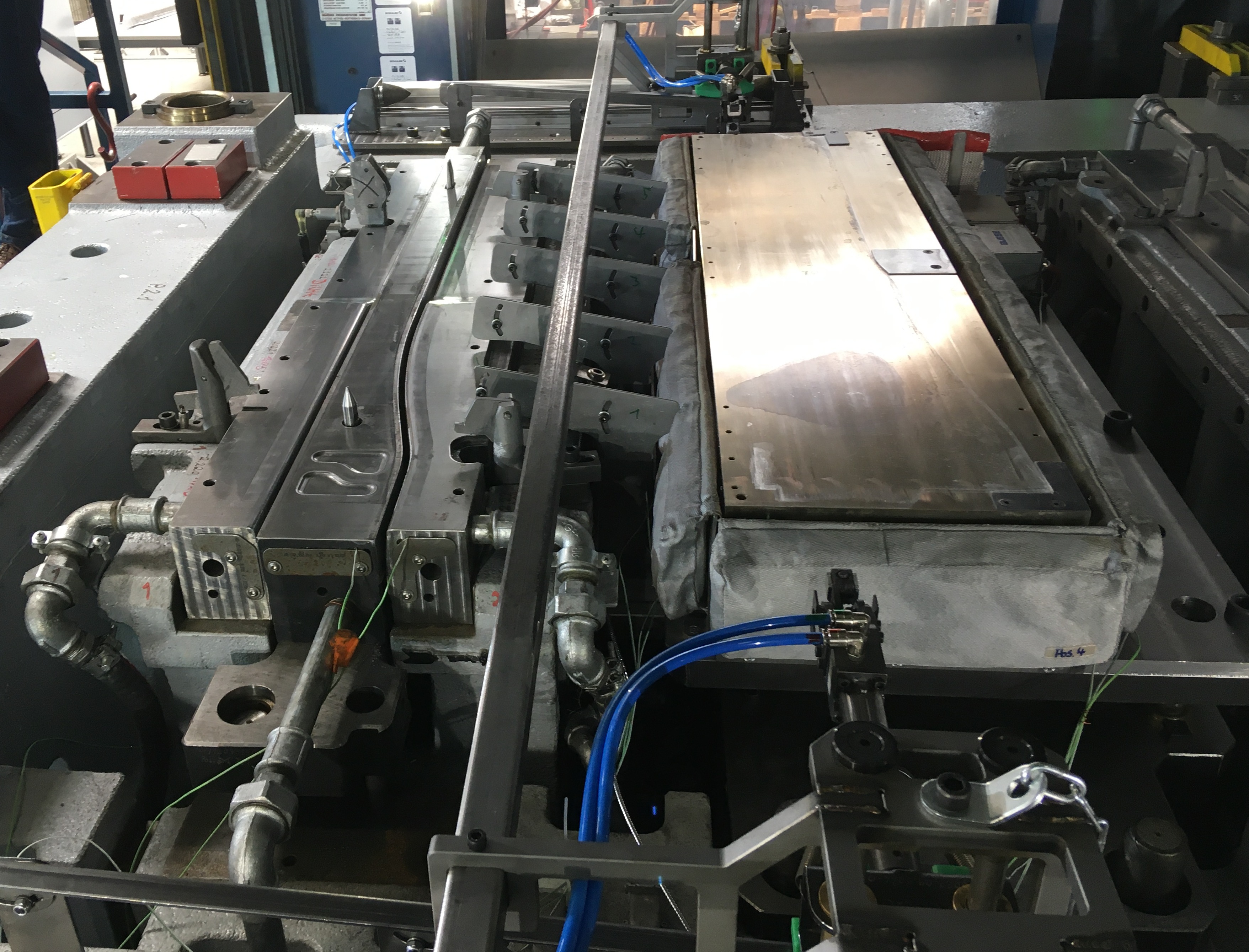
In the new process, the light metal is heated up very quickly (right), formed, and at the same time hardened. © Schuler
In the process, heating plates integrated into the first forming stage heat the 6 000 or 7 000 series aluminum sheet to over 300 to 450 degrees Celsius in a matter of seconds. In the second stage, the actual forming takes places in a water-cooled die while the next blank is already heating up at the same time. In a third and fourth stage, the part, which is still at about 60 degrees, can be cut.
On a 1 200 metric tons capacity hydraulic press from Schuler operating in conjunction with a highly dynamic three-axis transfer system, cycle times of just ten seconds per part can be achieved. In contrast to previous processes for hot stamping aluminum sheet, the components can be further processed immediately and do not require several hours of heat treatment to harden them. This noticeably reduces the production costs even further.
The first system is already being manufactured for an automotive supplier in Asia. The high-strength aluminum parts that will be produced on it are intended for a manufacturer of electric cars.
Schuler will present more on the new hot stamping process for aluminum and other solutions for metalforming technology at the Blechexpo trade show from November 7 to 10 in Stuttgart (Booth 8306).
Leave A Comment
You must be logged in to post a comment.