Hilchenbach, September 23, 2019. At the Blechexpo, ROEMHELD presents for the first time an element for the fully automatic clamping of dies on the press ram, which can measure real-time data on clamping forces and transmit them to the machine control. The new series of the rapid clamping system Flexline is therefore suitable for predictive maintenance and use in Industry 4.0 applications.

Components such as the magnetic clamping plates can be seen live in use during the exhibition on a “TOP Line 2000” press from Andritz Kaiser (photo: ROEMHELD).
Also, the company provides an overview of components for the efficient, fast and safe transport and change of heavy dies. On display are various transport carts, carrying consoles as well as roller or ball bars for machine tables.
ROEMHELD presents the clamping elements and components for optimising set-up times in sheet metal forming in Hall 8 at Stand 8507. A selection of the latest clamping and changing technologies can also be seen live in use on an Andritz Kaiser press during the exhibition at the manufacturer’s stand in the same hall.
Real-time data from the clamping element for condition monitoring
With a series of integrated sensors, the rapid clamping system Flexline determines process data on the press ram in real time and forwards it to the machine control. Thus, the operator receives information about the real clamping force on the die at any time and is immediately able to detect overloads on the clamping element, the occurrence of unusual tearing forces as well as die breakages and wear. The protocol of the clamping force progression facilitates error analysis and serves to solve problems quickly when servicing is required.
Thanks to a wide range of configuration options, the modular rapid clamping system Flexline can be used on almost all press models and for every die. It is suitable for both initial installation and retrofitting and is suitable for use in the automation of press lines.
Changing technology to optimise set-up times
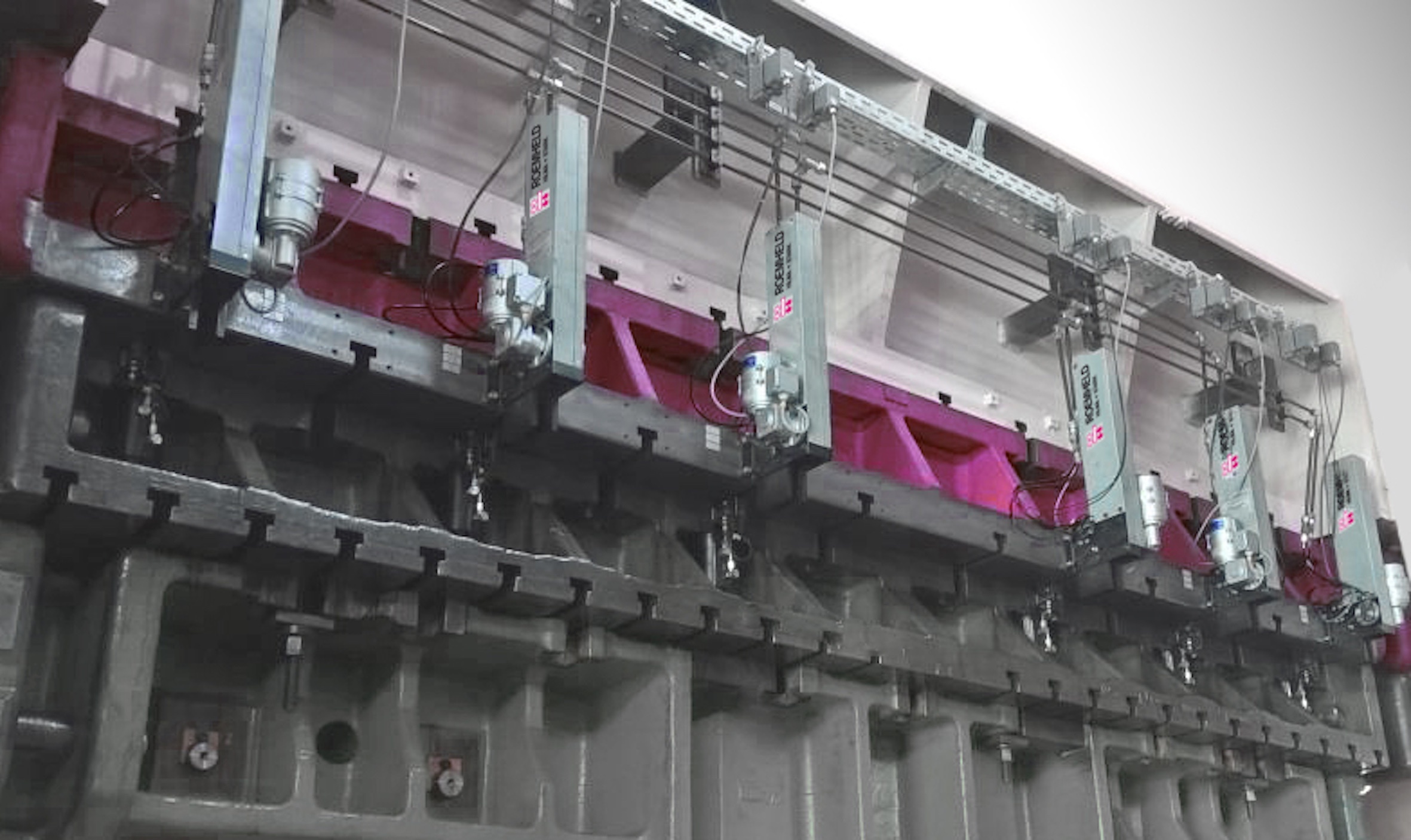
The rapid clamping system Flexline can measure real-time data on clamping forces on the press ram and transmit them to the machine control (photo: ROEMHELD).
The ROEMHELD Group will also show a selection of components for fast and safe change of heavy dies. They show four versions of transport carts for different loads up to a maximum of 1,600 kg. These can be used to move heavy loads quickly, effortlessly and ergonomically. On display at the stand are supported, hanging and swivelling carrying consoles which facilitate the insertion of dies into the press and the punching system.
The use of freely configurable ball and roller bars is particularly economical. They allow dies to glide easily over tables, surfaces and feeds, making them easy to slide and position. The trade fair presentation will be supplemented by a selection of hydraulic, mechanical, electro-mechanical and magnetic clamping elements.
Change technology live in use on an Andritz Kaiser press
Various components such as magnetic clamping plates, locking cylinders, carrying consoles and roller bars can also be seen live in use on a “TOP Line 2000” press from Andritz Kaiser, also in Hall 8 at Stand 8301, a few metres from the ROEMHELD stand.
ROEMHELD: Set-up time optimiser for sheet metal forming, plastic and rubber processing
With its extensive portfolio of die clamping technology, the set-up time optimiser ROEMHELD solves almost every clamping task in sheet metal forming, plastics and rubber processing. The magnetic, hydraulic and electro-mechanical clamping systems are highly versatile and contribute to making processes in single and series production of nearly all industries more efficient and economical. Products for die change such as die changing cart, roller bars and driven carrying consoles complete the product range.
About ROEMHELD:
Whether for aircraft, automobiles, machine tools or cases for smartphones: technologies and products of the ROEMHELD Group have been used to manufacture numerous industrial commodities and goods for end users for more than 60 years.
Efficient clamping technology solutions for workpieces, as well as for dies in forming technology and plastics processing, form the core of our ever-increasing portfolio. This is supplemented with components and systems for assembly and handling technology, drive technology and automation as well as locking mechanisms for rotors on wind energy systems.
In addition to a constantly growing range of more than 30,000 catalogue items, the ROEMHELD Group also specialises in the development and realisation of customised solutions and is internationally regarded as one of the market and quality leaders.
Innovation through tradition: ROEMHELD was established in 1707 with a foundry in Friedrichshütte, which still belongs to the ROEMHELD Group today and counts as one of the oldest active industrial businesses in Germany.
The owner-managed group of companies employs approximately 560 workers in its three locations of Laubach, Hilchenbach and Rankweil/Austria, and is represented in over 50 countries by service and sales organisations. With customers from the mechanical engineering sector, as well as the automobile, aviation and agricultural industries, the ROEMHELD Group generates an annual turnover of more than 110 million Euro.
Leave A Comment
You must be logged in to post a comment.